The Ultimate Guide to Square Wave 200 in Welding and Cutting Equipment
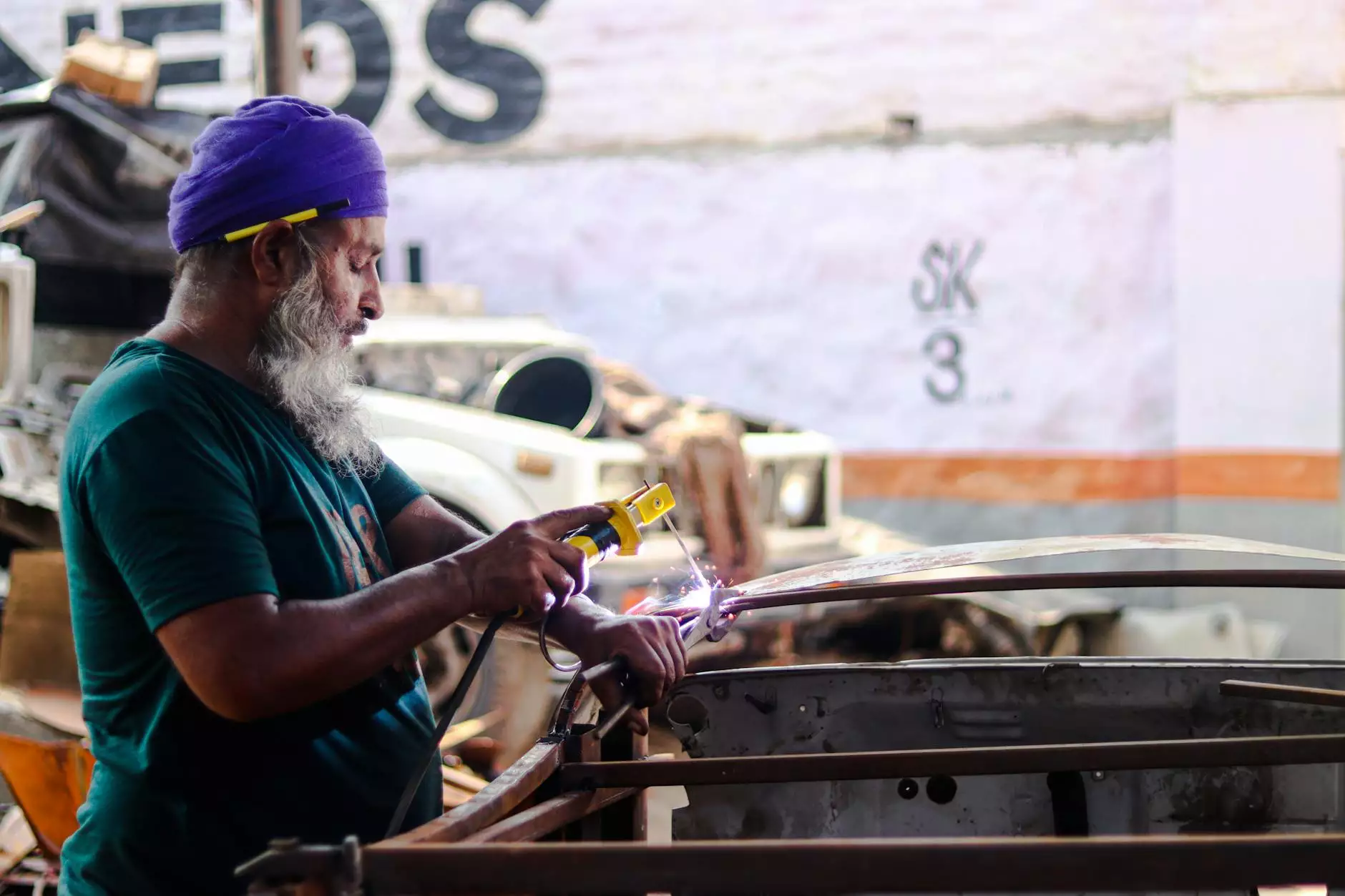
In the rapidly evolving world of welding and cutting technologies, the Square Wave 200 has emerged as a revolutionary solution that enhances both precision and efficiency. This article delves into the intricacies of the Square Wave 200, its applications, benefits, and how it stands out in the competitive market of welding and cutting equipment. As we explore this topic, we will emphasize why businesses, particularly in the realm of cutting and welding equipment, should consider integrating this technology into their operations.
Understanding the Square Wave 200 Technology
The Square Wave 200 is an advanced waveform technology utilized primarily in Tig welding processes. Unlike conventional sine wave welding, the square wave technology provides a more stable arc and a better overall performance. This technological shift allows for greater control over the welding process, ensuring superior penetration and bead appearance.
The Science Behind Square Wave
The Square Wave signal resembles a series of squares, which allows for distinct control over the arc characteristics. This results in the following advantages:
- Improved Arc Stability: The consistent power provided by the square waveform enhances stability, reducing the chances of arc extinguishing during the welding process.
- Enhanced Control: Welders can more finely tune their settings, allowing for adjustments in penetration and heat input, crucial for various materials.
- Better Cleaning Action: Particularly beneficial when welding aluminum, the square wave technology cleans the base metal effectively during the process.
Applications of Square Wave 200
The versatility of the Square Wave 200 makes it suitable for numerous applications in the cutting and welding industry, including:
1. Aluminum Welding
One of the standout capabilities of the Square Wave 200 technology lies in its suitability for welding aluminum. Aluminum presents unique challenges due to its reflective nature and susceptibility to burn-through. The square wave technology provides a high-frequency output that enhances the cleaning action of the arc, allowing the welder to create strong, clean welds even with thin aluminum sections.
2. Stainless Steel Fabrication
Stainless steel requires precise control to avoid warping and discoloration. The Square Wave 200 offers excellent arc control, ideal for fabricating intricate stainless steel components. The ability to adjust the waveform allows welders to minimize heat input, resulting in cleaner finishes with less distortion.
3. Industrial Applications
In the manufacturing, aerospace, and automotive industries, the stringent requirements for weld quality demand the best technology available. The Square Wave 200 provides consistency and reliability that companies can depend on for critical applications.
Benefits of Using Square Wave 200 Technology
Incorporating the Square Wave 200 into your cutting and welding operations offers significant advantages:
1. Cost-Effectiveness
Investing in the Square Wave 200 technology can minimize operational costs through:
- Reduced Material Waste: Precise control leads to fewer errors and better-formed welds, saving on additional material costs.
- Lower Rework Rates: High-quality welds decrease the necessity for rework or repairs, which can be time-consuming and expensive.
2. Enhanced Productivity
With the improved arc stability and control provided by the Square Wave 200, welders can complete tasks more efficiently, leading to increased productivity. Employers can accomplish larger volumes of work without compromising on quality.
3. Versatility
The technology's adaptability makes it possible to work with a wide range of materials and thicknesses. This versatility is crucial for businesses that handle diverse projects, allowing for a broad range of applications without the need for multiple sets of equipment.
Integrating Square Wave 200 into Your Business
For businesses looking to leverage the advantages of Square Wave 200 technology, the following steps can be taken:
1. Equipment Acquisition
Seek out reliable suppliers, such as tiendaguve.com, who offer a range of cutting and welding equipment featuring the Square Wave 200 technology. Ensure that the machines are compatible with existing tools and equipment in your arsenal.
2. Training and Development
Proper training is essential to maximize the benefits of this advanced technology. Provide comprehensive training sessions for your welding team to ensure they understand the nuances of the Square Wave 200 and can optimize its features for best results.
3. Maintenance and Support
Invest in regular maintenance schedules for the equipment to ensure longevity and optimal performance. Partnering with suppliers who offer excellent after-sales support can significantly enhance your operational efficiency.
Final Thoughts: The Future of Welding Technology
The Square Wave 200 technology represents a significant leap forward in cutting and welding processes. Its capabilities not only enhance the quality and speed of welding tasks but also contribute to the overall sustainability of production processes in various industries. Companies that adopt this technology will likely enjoy a competitive edge, higher productivity, and improved product quality.
As the welding industry continues to innovate, staying ahead with advanced technologies such as the Square Wave 200 will be key for businesses aiming to thrive in a demanding marketplace. Explore the offerings at tiendaguve.com to find the right solutions for your specific needs and start leveraging the advantages of square wave technology today!